The 5S methodology is an organisation technique for the workplace developed in Japan to increase productivity and job satisfaction in companies. Each one of the 5S involves a different stage in a process, which aims to eliminate the unnecessary aspects of production, by creating a cleaner and more pleasant workplace.
This management method is not just about cleaning or organisation. It is also about maximising efficiency in and benefits for companies.¹ The 5S framework emphasises the use of a specific mindset and tools to create efficiency and value. For this purpose, the 5S methodology involves observation and critical analysis. In addition, as an organisation method, it also allows for restricting stock, optimising production and reducing the risk of occupational incidents.
The 5S sequence2, 3
- Sort (Seiri 整理) – In this first phase, the essential materials for working are identified and classified, keeping only those items needed to complete tasks. The purpose of each tool or resource and the frequency at which it is used is analysed, in order to remove anything that may hinder or slow down work. Everything that does not help with completing a work-related process is eligible for removal from the work area. This frees up space and saves on production time for tools searching or cleaning the work area.
- Set in order (Seiton 整頓) – At this point, the necessary materials are organised and each item has a designated logical place. This phase accounts for who uses what item, when items are used and the best place to place them. The items can be grouped by categories or have tags. This prevents workers from wasting time on searching for tools. It also involves placing materials and resources in ergonomic locations where people will not have to make extra movements to reach them.
- Shine (Seiso 清掃) – Organising the workplace is just as important as keeping it clean. This step of the 5S system focuses on cleaning, which has a positive impact on the motivation to work and helps reduce workplace incidents. This phase also facilitates increased security in the workplace. It can involve routine tasks, such as washing, dusting or performing maintenance on machinery, tools, and other equipment.
- Standardise (Seiketsu 清潔) – Here, focus is placed on standardising processes and work procedures, so that workers are able to identify abnormal situations and correct failures. In essence, this is where the first three of the five phases come together. It is now possible to establish rules for how and when these tasks will be performed. For that, you can use schedules, charts, and checklists, as well as appoint people who will be responsible for carrying out different cleaning and organisational tasks.
- Sustain/self-discipline (Shitsuke しつけ) – Applying the 5S methodology involves carrying out systematic assessments and continuous work to maintain cleaning and organisation standards, as well as detecting new areas for improvement. Self-discipline allows users to get the most out of the five elements. In addition, this personal discipline involves a rigorous and effective application of the previous phases to ensure continuous monitoring of productivity levels.
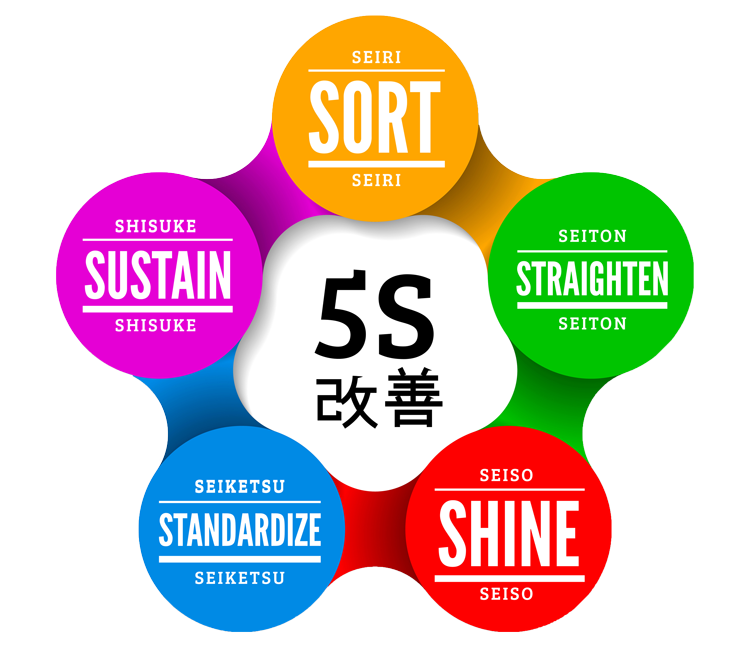
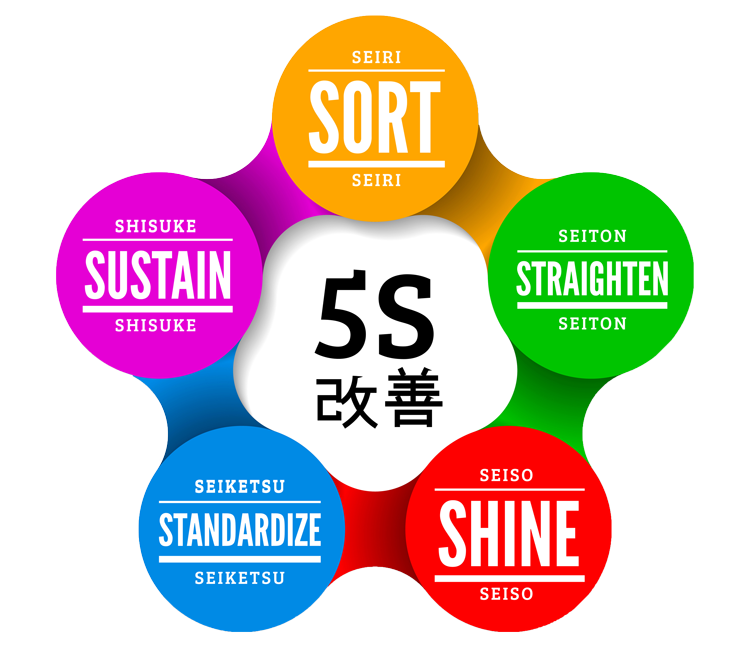
5S methodology in everyday work
As the above-mentioned phases may indicate, the 5S method is very practical and can show major results when applied correctly. It´s a methodology that requires systematic and strict monitoring, assessment and adjustment.
Here is feedback from Natalia Pérez, Administration General Service and Finance Support at Medline Iberia, on how she implements the 5S methodology in her daily work:
My ‘little obsession’ with orderliness and cleanliness, and some chapters of ‘The Home Edit: A Guide to Organizing and Realizing Your House Goals’ during the COVID-19 lockdown helped me to perform tasks that I have never done before. Work absorbs a large part of our day and we go through it without paying attention to the amount of things we store or forget we have. In addition, all these things take up quite a bit of space.
I have been in my current position for almost three months. When I arrive at the office, I organise everything by throwing away all that isn´t necessary to gain space. The key is to identify things that are out place with your naked eye. This is how the 5S methodology makes sense in my daily work. After this, it´s necessary to continue checking that everything is in order and maintain it.
The 5S methodology is about successfully reducing time and energy when performing a task. I think your company should try it. Don’t you? Begin improving your workers’ efficiency today!
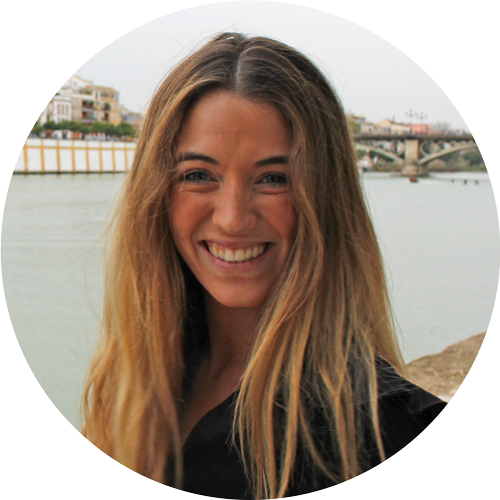
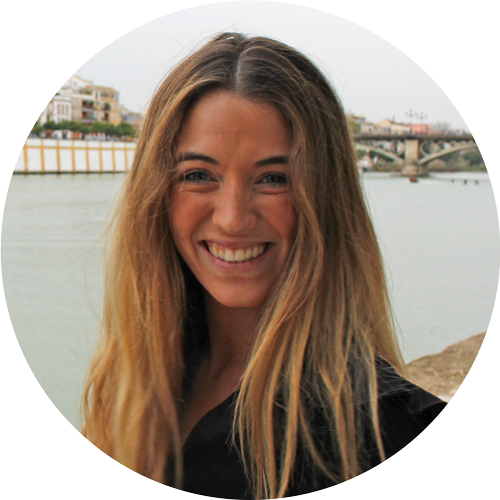
Paula Dalmau
Communications Coordinator Sales and Marketing, Medline Iberia
Paula is a passionate Spanish writer based in Madrid. Her interests are well-being, emotional intelligence and business topics. Her educational background is in journalism, advertising, public relations and digital marketing. Learn more on LinkedIn.